HARDWOOD FLOORING
Hardwood is a timeless, gorgeous flooring choice that will add value to any home.
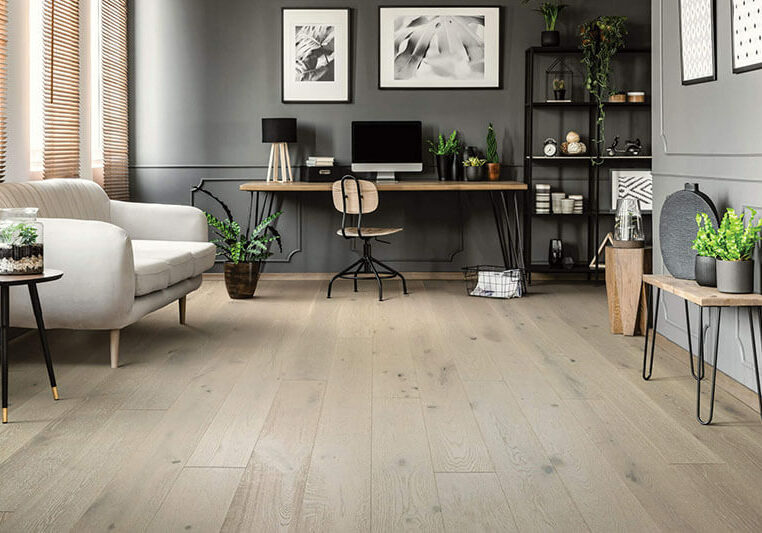
Quality Hardwood For New Homes
Create gorgeous, timeless living spaces while adding value to your home with hardwood flooring. Hardwood has remained sought-after for centuries because of its natural beauty, textures, and characteristics that enhance the overall look of any home. Warm and inviting, hardwood is a classic flooring choice that homeowners will love.
At The L&L Company, we carry quality flooring from the top manufacturers to provide you with the latest designs and best hardwood currently available. Our hardwood flooring will remain pristine for many years.
We are the preferred hardwood flooring provider for builders in the Mid-Atlantic, and we look forward to working with you.
Why Choose Hardwood Flooring?
Hardwood is available in a wide selection of options, from different tones, finishes, textures, species, and plank sizes, so you can create a custom space that matches the aesthetic of any home. Hardwood remains a popular flooring choice for homeowners for centuries because of its natural beauty and longevity.
Hardwood is durable, and with the right care can last a lifetime. You cannot go wrong installing hardwood to create beautiful spaces homeowners will love.
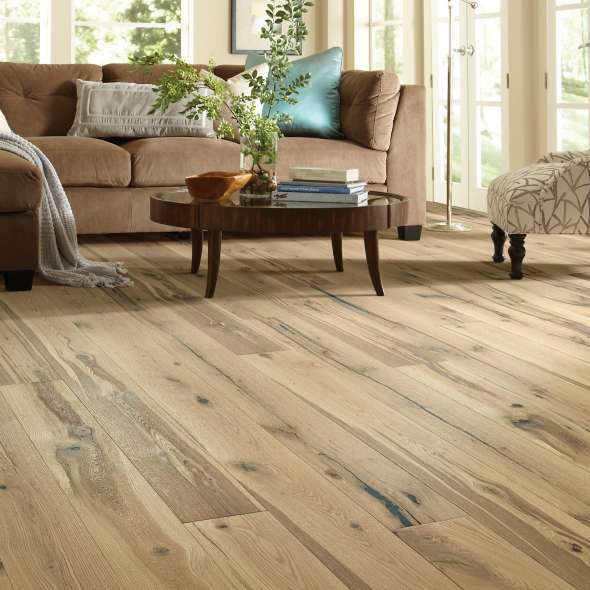
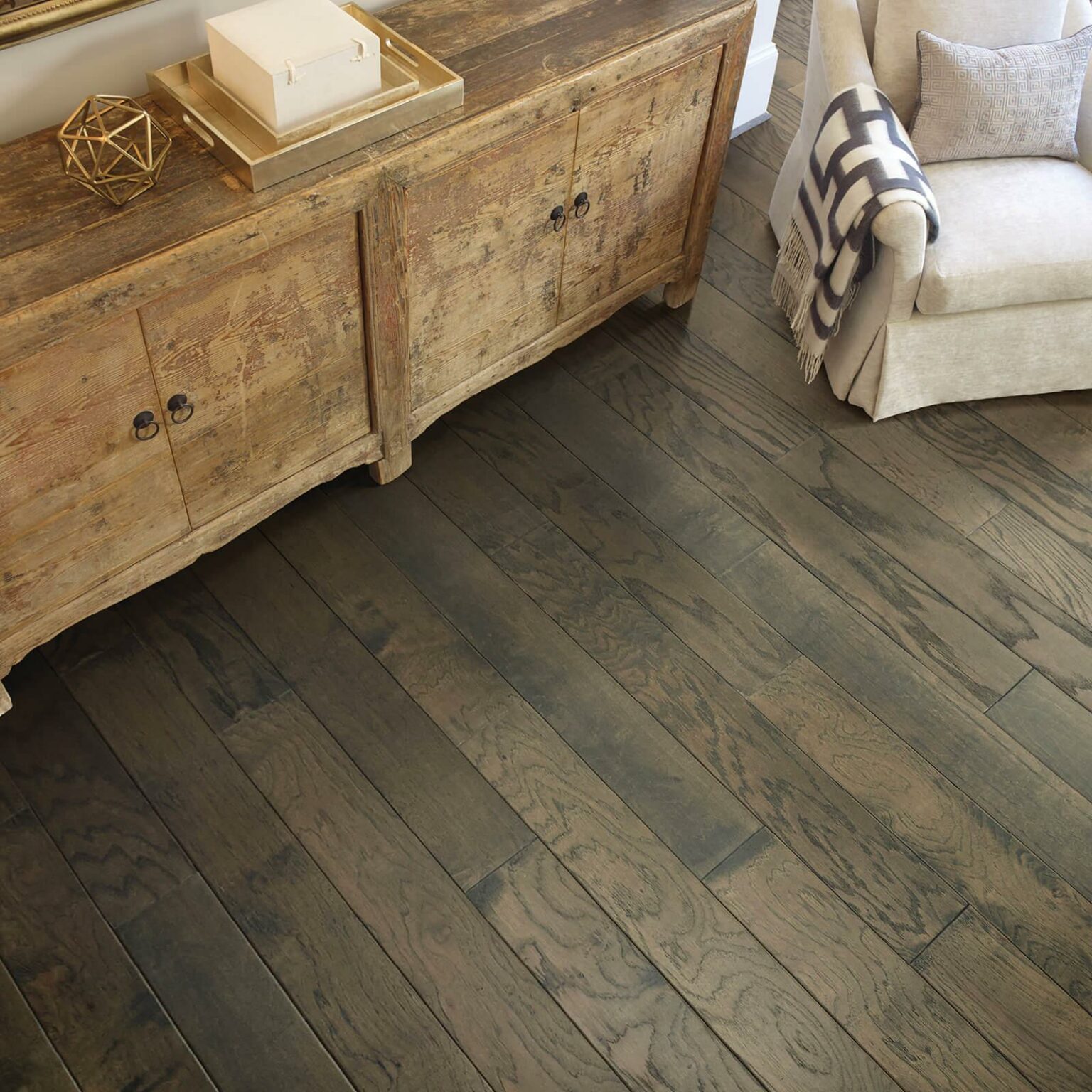
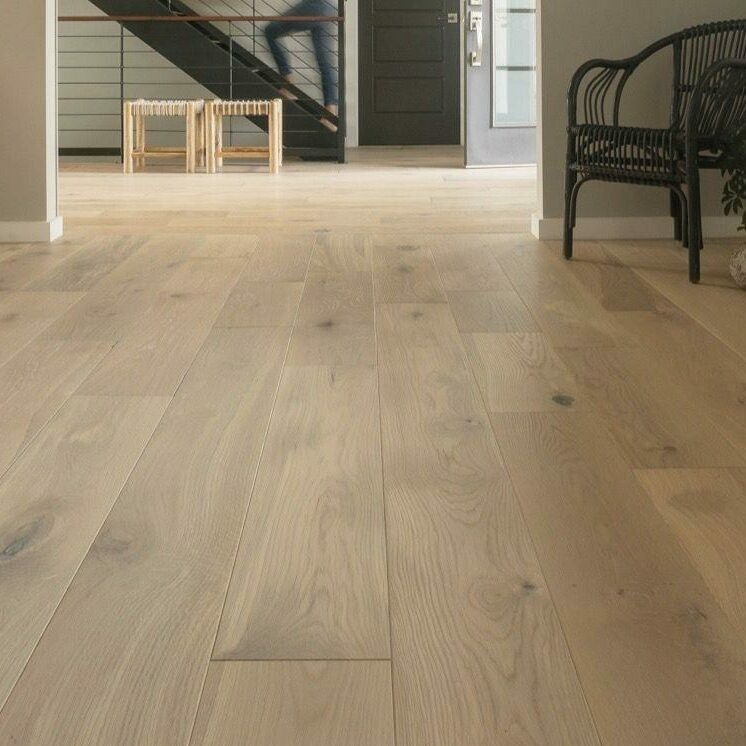
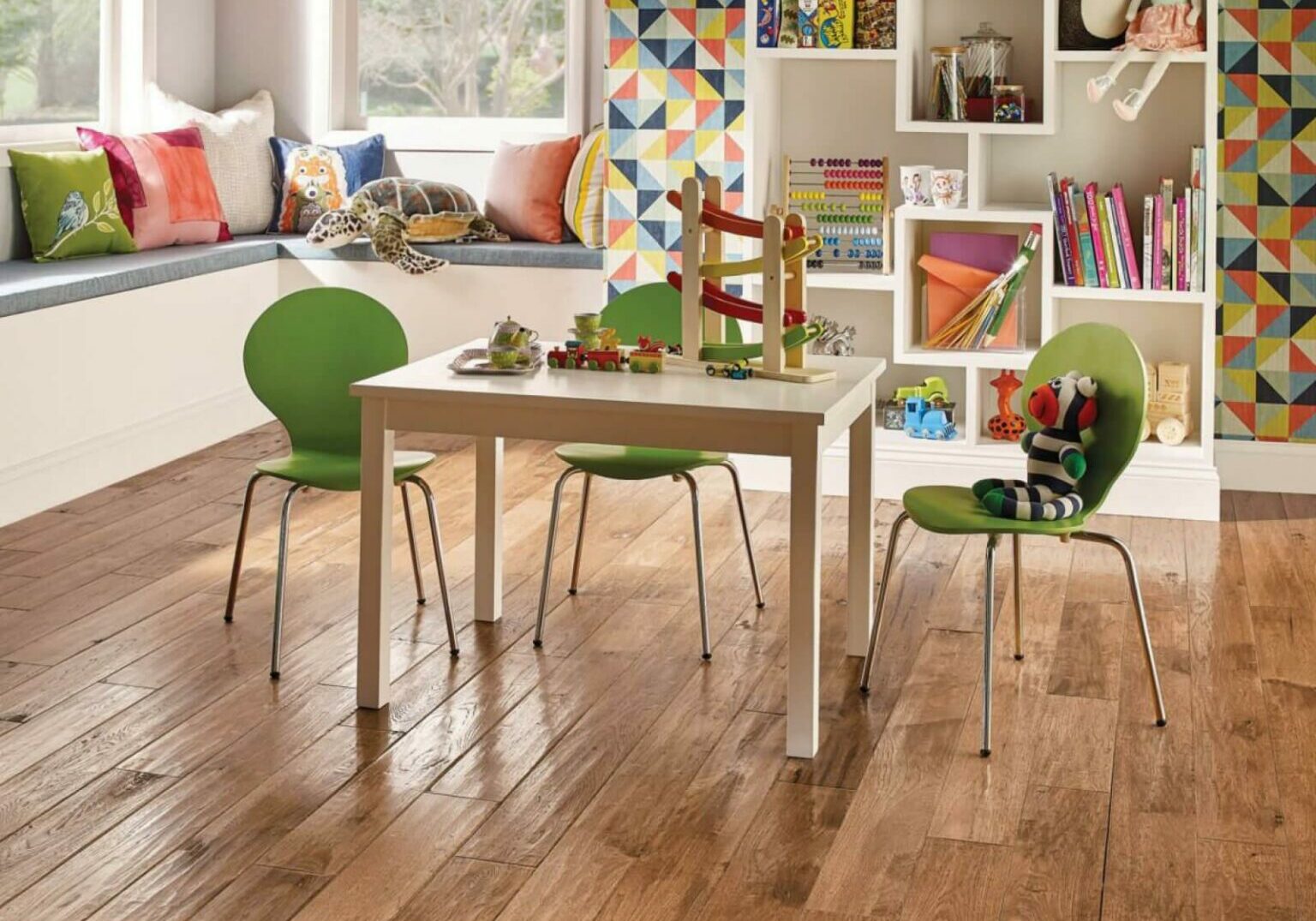
Need Inspiration?
Take a look at our hardwood inspiration gallery before shopping for hardwood flooring! See the latest trends and more.
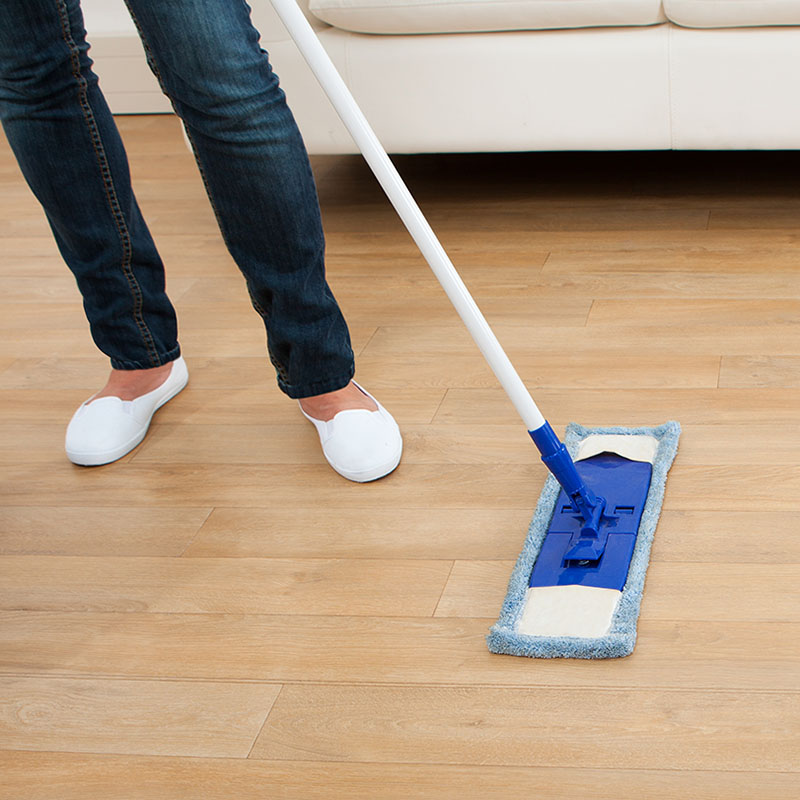
Hardwood Care & Maintenance
With the right care, hardwood flooring will last a lifetime. Learn how to properly care for it with our guide.
Learn More About Hardwood
Before you Buy
Before you purchase hardwood, know this.
Nothing motivates people to learn about something than when they have to invest a sizeable sum to purchase it.
Buying hardwood flooring is no exception.
It pays, today and tomorrow, to know not only the basics but some of the specifics.
In the journey to finding the right flooring for your home, understanding things like hardwood characteristics, traits and quirks can be invaluable.
That’s why we offer you this section.
It’s a summary of many of the things you should know about hardwood before you open your checkbook or get out the charge card.
Know this about Finish in Place hardwood. Nature’s rich beauty is abundant when displayed through the character of a Finish in Place hardwood floor.
In addition to various wood species and finishes, these hardwood planks are also available in different widths – an elegant addition to any home.
Finish in Place, or unfinished hardwood, is installed in the home and then sanded. The stain and 2-3 coats of urethane finish are then applied. The urethane finish, brushed or mopped on, is known as a “floor finish” not a “furniture finish”.
Dust is a fact of life and finishing.
Since your floor is being finished in your home, please be aware that your floor will not be “dust free” as it is impossible to create a “dustless” environment.
Some dust will fall onto the freshly applied topcoat of urethane finish.
You may also see sanding marks, small bubbles and brush marks.
However, take heart, Finish in Place floors may be screened and recoated to rejuvenate the finish and revitalize the floor’s natural beauty.
The different hallmarks of hardwoods.
Each species of wood has its own unique characteristics. Color is determined by what part of the tree the wood originally comes from.
The grain pattern is determined by the species and how the wood is cut.
Natural variations in the color and grain are normal and to be expected. Similar to natural stone, these variations create the beautiful and unique look of a wood floor. They make your floor close to one of a kind. Understand that wood moves, naturally.
Wood floors will expand and contract due to moisture and temperature changes, causing hairline cracks, slight height variations or both.
Hardwood does not expand or contract equally in all directions. This is not considered a defect but a natural result of nature.
So, in dry climates, you may want to consider the use of a whole house humidifier to help minimize shrinkage and hairline cracking.
Here are the facts about subfloors.
No subfloors are perfectly level. You may also hear hollow sounds where your subfloor’s surface dips and ridges.
This does not affect the integrity or installation of the hardwood. Hollow sounds are normal and are not considered a product or installation defect.
All hardwood floors will fade, darken or change shades over time. Exposure to sunlight will greatly increase this process.
Window treatments are recommended as well as rotating area rugs and furniture regularly to allow floors to age evenly from UV exposure. Pre-finished hardwood pre-buying notes.
A work of natural art, the elegance of a pre-finished hardwood floor adds beauty and value to any home, easy care and durability to any lifestyle.
Each species of wood has its own unique characteristics and the conditions of nature that the wood matured in make each floor exceptional and individual.
Pre-finished hardwood floors are sanded, screened and stained in highly efficient manufacturing plants.
Several coats of urethane are sprayed on the boards and then they are UV dried for a very durable finish.
Pre-finished floors may be screened and recoated to rejuvenate the finish and revitalize the floor’s natural beauty. Pre-finished hardwood information on color, grain pattern, expansion and contraction, subfloor leveling and floor protection is the same as the information under Finish in Place hardwood, above. Get on top of the bottom line. Know the entire cost of ownership.
The “cost per square foot” of your hardwood floor is just one component of the entire project cost. To ensure there are no surprises, and the hardwood you select fits within your overall project budget, be sure to ask us to calculate the total cost of your floor covering project.
Here’s a list of potential additional expenses you may incur:
- Furniture removal/replacement.
- Demolition/disposal of old floor covering. Depending on the existing floor covering, this can be an expensive item; also, be sure to include the cost to dispose of the old floor covering.
- Subfloor preparation. Depending on the condition of the subfloor, it may require additional work.
- Product delivery.
- Hardwood installation. Determine the cost per square foot to install it.
- Materials required to complete the installation. Your new hardwood floor may require additional materials to install it properly.
We can help you answer questions regarding the manufacturer’s warranty and care guide for directions on how frequently the floor should be cleaned and the cost to clean it.
There’s a lot to know and keep in mind before buying a hardwood floor, but it’s well worth the effort. If you’re a smart and knowledgeable shopper it will pay off in many ways, the best of which will be hardwood flooring you’re proud to come home to.
How it's Made
Easy, concise knowledge about hardwood construction.
Understanding how hardwood is made is easy, and, here, efficient. We’ve explained all the basics in this section and urge you to check them out.
Knowing how hardwood is constructed provides you with an understanding of the hardwood floor right from its beginning.
That’s important information because these are the materials you’ll be living with and walking on for years to come should you choose this flooring product.
Knowing the different types that make up various hardwood floors also helps you understand and evaluate their performance aspects: why certain hardwoods are easier to install, why some wear better, longer, and why others are easier to replace.
Plus, perhaps most important, understanding hardwood construction and materials can make you a smarter shopper, help you better determine hardwood flooring value and keep you within the parameters of your budget. Understanding hardwood sizes, species and types.
When we think of solid wood floors we generally are talking about a 3/4" thick plank that is 2 1/4" wide.
This is the classic strip wood floor, although it is possible to find a narrower width or a slightly thinner gage. The strips are generally in random lengths from 12" – 84".
The most common wood species used for solid strip floors are red oak, white oak, maple, cherry, white ash, hickory or pecan.
And the three common types of wood floors are Solid, Engineered and Longstrip Plank.
Type 1: think solid and expansive.
Solid wood floors are one solid piece of wood that have tongue and groove sides. When we talk about solid wood floors, we tend to think of floors that are unfinished, but it’s important to know that there are also many pre-finished 3/4” solid wood floors. And you should also be aware of the moisture factor.
Solid wood floors are sensitive to moisture and because so they are used in nail down installations and are not recommended for installation below ground level, or directly over a concrete slab.
The good news is that these floors can be refinished, or recoated, several times, which adds to their appeal and to their long life in your home.
In fact, there are solid floors that are over 100 years old that are still in good condition with rich patina and character – enhancing the beauty of the home.
Because they’re a natural product, hardwood flooring will expand and contract in response to seasonal changes in moisture. In the winter heating months, moisture leaves the wood causing the floor to contract, which creates small gaps between each plank.
In the summer months, when the humidity is higher, the wood will expand and the gaps will disappear. If there is too much moisture it may cause the wood planks to cup, or buckle. Not something you want in your home.
This is why it is important when installing a solid strip floor to leave the proper expansion area around the perimeter and to acclimate the wood prior to installation. This will help assure a lasting, beautiful application. Know that oak is a wood of choices.
Oak is commonly used for solid unfinished wood floors and there are several different qualities of oak for you to choose from.
These qualities are clear, select and better, #1 common, and #2 common.
The clear has no visual blemishes or knots and is extremely expensive. While the select and better quality has some small knots and very little dark graining.
The #1 common and #2 common have more knots and more dark graining. So be aware of that when buying an unfinished solid oak floor and make sure you know which quality of wood you are buying.
Type 2: the efficient, engineered solution.
Engineered wood floors are generally manufactured with 2, 3, or 5 thin sheets or plies of wood that are laminated together to form one plank.
These wood plies are stacked on top of each other but in the opposite directions. This is called cross-ply construction which creates a wood floor that is dimensionally stable and less affected by moisture than a 3/4” solid wood floor.
In the presence of moisture, solid wood planks will always expand across the width of the planks, rather than down the length of the boards.
The advantage of cross-ply construction allows the plies to counteract each other which will stop the plank from growing or shrinking with the changes in humidity.
The other advantage for you is versatility. You can install these floors over concrete slabs in your basement as well as anywhere else in your home.
Most engineered floors can be nailed down, stapled down, glued down, or floated over a wide variety of subfloors, including some types of existing flooring.
Engineered floors will range from 1/4" to 9/16" in thickness, and vary from 2 1/4" to 7" in width. The widths can also be mixed, such as 3-5-7-inch planks installed side by side. By varying the board widths you can change the total appearance of the floor. Create a truly custom look for your home. The lengths will be random and range from 12" – 60" in length. For flexibility, engineered is top-notch.
Because engineered wood floors are made up of several layers of wood the top finish layer can be a totally different wood species. A variety of domestic or exotic hardwood species are available such as Oak, Maple, Hickory or Cherry.
Type 3: the easy-to-replace longstrip.
Longstrip plank floors are similar to engineered floors and have several wood plies that are glued together.
The center core is generally a softer wood material and is used to make the tongue and groove. A hardwood finish layer is glued on top of the core.
The top layer can be almost any hardwood species and is made up of many smaller individual pieces that are laid in three rows.
Longstrip planks are approximately 86" in length and 7 1/2" in width. They generally have between 17 and 35 pieces that make up the top layer of each board.
This gives the effect of installing a board that is 3 rows wide and several planks long. Each longstrip plank looks like an entire section that has already been pre-assembled for you. This alone can create a unique look all your own.
Longstrip planks are designed for the floating installation, but most can also be glued-down, or stapled down. Because these floors can be floated they are extremely versatile – they can go over a wide variety of subfloors and on any grade level.
Like engineered floors, longstrip floors come in a wide variety of domestic and exotic hardwood species.
Longstrip plank floors have another advantage. When damaged, they are easy to replace. That can be an important consideration for active homes.
Those are the ins and outs of hardwood construction.
We hope this knowledge makes you a smarter shopper, helps you narrow down your options, or even solidifies your choice of hardwood flooring for your home.
- made with 2,3, or 5 thin sheets laminated to form 1 plank
- plies stacked in opposite directions- cross-ply construction
- cross ply - dimensionally stable, less affected by moisture than 3/4” solid
- with moisture, solid planks expand across width not down length
- cross-ply advantage: plies counteract for plank growth, shrinking with humidity changes
- versatile: installed over concrete slabs or other places
- installed by: nailed down, stapled down, glued down, or floated
- over a wide variety of sub-floors, and some existing floors
- range: 1/4" to 9/16" thick
- width:2 1/4" to 7", mixed (3-5-7-inch planks installed side by side)
- varying widths can change the appearance
- lengths random: 12" – 60" in length
- made of layers - top finish layer is different species
- domestic or exotic species: Oak, Maple, Hickory or Cherry
Type 2: Solid
- one solid piece with tongue and groove sides
- unfinished and pre-finished 3/4” solid
- moisture factor: sensitive to moisture
- used in nail down installations
- not recommended for below ground level, or over a concrete slab
- can be refinished, or recoated, several times
- natural product: expand and contract with season changes (moisture)
- in winter heating months, moisture leaves the wood causing contraction this creates gaps between planks
- in summer months, with high humidity, wood expands meaning gaps disappear
- too much moisture causes planks to cup, or buckle
- important to leave expansion around the perimeter
- important acclimate prior to installation
- Oak: used for solid unfinished floors - several qualities to choose from
- clear-no visual blemishes or knots, expensive
- select and better- some small knots, little dark graining
- #1 common, #2 common - more knots and dark graining
Type 3: Longstrip
- similar to engineered floors
- several wood plies glued together
- center core is softer, used to make the tongue and groove with finish layer on top of the core
- top layer: any species made up of smaller individual pieces laid in 3 rows
- 86" in length and 7 1/2" in width
- 17 and 35 pieces making up the top layer of each board
- each plank looks like a section already pre-assembled
- designed for the floating installation
- can be glued-down, or stapled down
- extremely versatile – can go over a variety of sub-floors and grade level
- come in a wide variety of domestic and exotic species
- advantage: when damaged, they can be replaced easily
hardwood Styles
Basic knowledge about hardwood styles and personalities.
Knowing someone’s style can tell you many things about him or her. The same goes when shopping for hardwood flooring.
Understanding the types, species and finishes of hardwood products can provide you with valuable information, let you shop smarter and compare with confidence.
In this section you’ll learn all about the wide array of hardwood styles on the market today. In fact, there are so many design options available you can create a hardwood floor that matches both your lifestyle and your desire for beauty, durability and practicality.
For example, inserting decorative medallions, running the boards on the diagonal, or creating a border are just some of the designs one can consider.
But before you get to the design, you need to know how to select the type of hardwood that’s right for you and your home.
Today you can choose between a pre-finished hardwood floor and one that is unfinished.
Pre-finished hardwood comes ready for installation in your home. The hardwood boards have already been sanded, stained and finished at the manufacturing plant. In many cases this can provide a harder, better- protected surface.
Pre-finished floors offer a wider variety of wood species and save hours of labor and cleanup.
But unfinished wood floors allow you to have a custom job – you choose the wood species and it’s sanded and the stain is applied on site. With unfinished you also have the chance to level the surface of the entire floor after it has been installed.
You get an extended factory finish warranty with pre-finished floors, but not with most job-site finishes
Location is consideration No. 1.
To begin with, you need to look at where you plan on installing your new wood floor.
There are limitations on where some wood floors can be installed. This is especially true for the 3/4" solid wood floors.
Solid hardwood floors are more susceptible to moisture and are generally not recommended for basements, or installing directly onto a concrete slab.
Be in the know about grain and cut.
Hardwood styles are the result of the wood species available. Some of the more common species are red oak, white oak, maple, cherry, white ash, hickory or pecan.
Each species has its own unique graining and texture. The graining on the boards is determined by the way it has been cut.
There are two cutting processes. “Sliced Cut” shows a more uniform pattern, whereas “Rotary Cut” displays a larger and bolder graining pattern.
Keep color in mind.
Within each species of hardwood you will have a choice of color and finishes. Here’s where it pays to shop carefully.
When selecting a color, choose one that either coordinates or contrasts with your cabinetry and furniture.
Also keep in mind that darker woods tend to be more formal while natural colors are more casual.
Which finish?
You should be aware that there are different types of finishes depending on whether your hardwood floor is pre-finished or job site finished.
In general, lower gloss levels are better suited for active rooms. This is because lower gloss or matte finishes help minimize the appearance of dirt and scratches.
Consider the elegant look of the high gloss finish for a more formal décor.
Upkeep is no big deal.
The days of having to wax and scrub your hardwood floors are pretty much gone forever. Manufacturers of pre-finished wood floors have developed sophisticated techniques to quickly apply hard, durable, urethane-based finishes right at the factory.
By using ultra violet lights the pre-finished wood planks can have several coats of urethane applied within a matter of a few minutes. This is helping make hardwood floors both more affordable, and much easier to maintain.
Recently, the hardwood flooring manufacturers have begun to add small chips of Aluminum Oxide directly to the floor's finish which dramatically increases the life of the urethane finish.
Protection lies in numerous coats.
Most factory finished hardwood floors have several coats of finish applied to the wood's surface. As example, many wood floor companies are applying 6-10 coats of a ultra-violet (UV) cured urethane. This would be extremely difficult for someone to duplicate on a job site finish, not to mention how many days it would take.
This is one of the reasons why many flooring mechanics, flooring retailers, and builders are pushing pre-finished hardwood floors. Instead of taking several days to install and finish a new hardwood floor a pre-finished hardwood floor is generally done in one day.
This does not mean you should wash your floor with a mop, but it does mean these floors won't watermark like the old waxed hardwood floors. The UV cured urethane wood finishes do make these floors easier to maintain than the old waxed hardwood floors.
Factory Pre-finished hardwood finishing comes in many forms:
- UV-cured – Factory finishes that are cured with Ultra Violet lights versus heat.
- Polyurethane – A clear, tough and durable finish that is applied as a wear layer.
- Acrylic-urethane – A slightly different chemical make up than Polyurethane with the same benefits.
- Ceramic – Advanced technology that allows the use of space-age ceramics to increase the abrasion resistance of the wear layer.
- Aluminum Oxide – Added to the urethane finish for increased abrasion resistance of the wear layer, which is becoming extremely popular on the better grade wood floors.
- Acrylic Impregnated – Acrylic monomers are injected into the cell structure of the wood to give increased hardness and then finished with a wear layer over the wood.
Job-site hardwood flooring finishing methods are also available.
If you want a custom stained hardwood floor, or a wood floor to match existing trim, than a job-site finish is your answer.
Job-site finish means you start with a bare (unfinished) hardwood floor and than the floor is sanded, stained, and finished in the home.
The other advantage of a job-site finish is, if you are concerned with uneven heights between planks, the sanding process will smooth out the floor. Be warned, though, this can be quite a mess and the process does take several days.
Job-site hardwood floor finishing methods include:
- Water Based Urethane – Water is used as part of the chemical make up of the polyurethane finish.
- Solvent Based Urethane – Oil is used as part of the chemical make up of the polyurethane finish.
- Moisture Cured Urethane – A similar chemical make up as solvent based urethanes, but this finish needs the humidity (moisture) in the air to cure.
What to know about board widths.
When shopping for a hardwood floor you will see boards in various sizes.
The narrower board widths are referred to as “strips” and the wider units as “planks.”
You should be aware that board width can visually impact a room.
Narrow width boards will expand a room, while wider boards work well in a larger room or area.
All about edges.
Different hardwood floors have different edges. Hardwood floors come in either a beveled edge, or a square edge.
Today, most hardwood floor manufacturers are calling their beveled edge "eased edge" because the tapered edge is dramatically reduced from the old deeply grooved edges.
The beveled edges do serve a purpose. The manufacturer can produce beveled edge planks faster than square edge, which in turn lowers their production costs.
Also, a beveled edge floor is more forgiving when installed over irregular subfloors and you don't have the problem of overwood (uneven plank heights abutting each other).
To help you understand hardwood edges, here’s a summary of today’s types: Square Edge:
The edges of all boards meet squarely creating a uniform, smooth surface that blends the floor together from board to board. The overall look of this floor gives a contemporary flair and formal feeling to the room.
Eased Edge:
Each board is just slightly beveled. Some manufacturers add an eased edge to both the length of the planks as well as the end joints. Eased edges are used to help hide minor irregularities, such as uneven plank heights. Eased edge is also called micro-beveled edge.
Beveled Edge:
These products have a very distinctive groove in them. Beveled edge planks lend themselves to an informal and country decor. With the urethane finishes applied at the factory today, the beveled edges are sealed completely, making dirt and grit easy to be swept or vacuumed out of the grooves.
Rating the hardness of wood. Below are listed the relative hardness for numerous wood species used in flooring.
These ratings were done using the Janka Hardness Test, which measure the force needed to embed a .444 inch steel ball to half its diameter in a piece of wood.
The higher the number the harder the wood. Although this is one of the best methods to measure the ability of wood species to withstand indentations, it should be used as a general guide when comparing various species of wood flooring.
The construction and finish also play an important role in the durability and ease of maintenance of any wood floor.
Species Guide Red Oak
Red Oak is the most abundant growing species in the United States. The sapwood of Red Oak is white to light brown while the heartwood has a pinkish reddish brown tone. It comes in four different grades:
Quartersawn
highest quality with almost no knotholes or color deviation. Smooth Finish suggested.
Quartersawn Select
Second highest quality with few knotholes and very slight color deviations. Smooth finish suggested.
Select #1 Common
Third highest quality with more pronounced knotholes and color deviations. Suggest hand scraped or smooth.
common 1 #2 Common
Lowest quality with many knotholes and color deviations. Suggest hand scrape only.
White Oak
White Oak is similar to Red Oak but is slightly more dense and has longer rays. The sapwood is light colored and the heartwood is light to dark brown. White Oak comes in the same four grades as Red Oak: Quartersawn
highest quality with almost no knotholes or color deviation. Smooth Finish suggested.
Quartersawn Select
Second highest quality with few knotholes and very slight color deviations. Smooth finish suggested.
Select #1 Common
Third highest quality with more pronounced knotholes and color deviations. Suggest hand scraped or smooth.
Common 1 #2 Common
Lowest quality with many knotholes and color deviations. Suggest hand scrape only.
Cherry
American Cherry grows primarily in the Midwestern and Eastern United States and is very hard and dense. The sapwood varies from a rich red to reddish brown and will darken with age. The sapwood tends to be a creamy white.
Hickory/Pecan Hickory is the hardest, heaviest, and strongest American wood. The sapwood of hickory is white and the heartwood is pale to reddish brown. It can be finished smooth or hand scraped.
Maple Growing in the Pacific Northwest, maple tends to be light but a very dense wood. Generally there is no marked difference between the sapwood and heartwood. Because of its density, maple is not recommended for high humidity areas. Smooth Finish suggested.
Pine Tends to be a soft wood that absorbs moisture very well and is recommended for high humidity areas. The sapwood in pine is usually light yellowish-white while the heartwood tends to be yellowish-orange. Can be finished smooth or hand scraped.
Reclaimed Pine Same characteristics as Pine, however it is recycled from old buildings (usually barns).
Walnut Walnut grows primarily in the Eastern United states. The sapwood tends to be white while the heartwood ranges from a deep chocolate to purplish black. Walnut is great for borders and is finished smooth.
Mesquite Mesquite grows primarily in the Southern United states and is known for being a very hard and durable wood. The sapwood tends to be pale while the heartwood is reddish brown. Mesquite usually contains lots of knotholes and a smooth finish is recommended.
HARDNESS RATING
- Douglas Fir 660
- Southern Yellow Pine (shortleaf) 690
- Southern Yellow Pine (longleaf) 870
- Black Cherry 950
- Teak 1000
- Black Walnut 1010
- Heart Pine 1225
- Yellow Birch 1260
- Red Oak(Northern) 1290
- American Beech 1300
- Ash 1320
- White Oak 1360
- Australian Cypress 1375
- Hard maple 1450
- Wenge 1620
- African Pedauk 1725
- Hickory 1820
- Pecan 1820
- Purpleheart 1860
- Jarrah 1910
- Merbau 1925
- Santos Mahogany 2200
- Mesquite 2345
- Brazilian Cherry 2350
Understanding the hardwood family should help you decide if this is a flooring answer for you and your home. At the very least, we hope this section has increased your knowledge of hardwood, one of the most beautiful, inviting and enduring flooring options around.
hardwood Glossary
For definitions of other terms not listed here, please go to these sections: How It’s Made, Styles, Before You Buy and Installation.
Above Grade
Any floor that is above the level of the surrounding ground on which the structure is built.
Acrylic Impregnated
Acrylic monomers are injected into the cell structure of the wood to give increased hardness and then finished with a wear layer over the wood.
Acrylic Urethane
A slightly different chemical make up than Polyurethane with the same benefits.
Aluminum Oxide
Added to the urethane finish for increased abrasion resistance of the wear layer, which is becoming extremely popular on the better grade wood floors.
Below Grade
A cement slab poured below the level of the surrounding terrain.
Better
A quality of oak. Better Oak has some small knots and very little dark graining.
Beveled Edge
These products have a very distinctive groove in them. Beveled edge planks lend themselves to an informal and country decor. With the urethane finishes applied at the factory today, the beveled edges are sealed completely, making dirt and grit easy to be swept or vacuumed out of the grooves.
Buckle
In the summer months, when the humidity is higher, wood will expand and gaps will disappear. If there is too much moisture it may cause the wood planks to cup, or buckle.
Ceramic
Advanced technology that allows the use of space-age ceramics to increase the abrasion resistance of the wear layer.
Clear
A quality of oak. Clear Oak has no visual blemishes or knots and is extremely expensive.
Cross-ply Construction
Engineered wood plies that are stacked on top of each other but in the opposite direction is called cross-ply construction. This creates a wood floor that is dimensionally stable and less affected by moisture than a 3/4” solid wood floor. Cross-ply construction allows the plies to counteract each other which will stop the plank from growing or shrinking with the changes in humidity. The other advantage for you is versatility. You can install these floors over concrete slabs in your basement as well as anywhere else in your home.
Cupping
A type of warping with a concave condition; the sides are higher than the center.
Eased Edge
Each board is just slightly beveled. Some manufacturers add an eased edge to both the length of the planks as well as the end joints. Eased edges are used to help hide minor irregularities, such as uneven plank heights. Eased edge is also called micro-beveled edge.
Engineered
One of the three common types of wood floors. (Others are Solid and Longstrip Plank.) Engineered wood floors are generally manufactured with 2,3, or 5 thin sheets or plies of wood that are laminated together to form one plank. Most engineered floors can be nailed down, stapled down, glued down, or floated over a wide variety of subfloors, including some types of existing flooring.
Finish in Place
Finish in Place, or unfinished hardwood, is installed in the home and then sanded. The stain and 2-3 coats of urethane finish are then applied. The urethane finish, brushed or mopped on, is known as a “floor finish” not a “furniture finish”. Finish in Place floors may be screened and recoated to rejuvenate the finish and revitalize the floor’s natural beauty.
Floating Floor Installation
With the floating installation method the floor is not mechanically fastened to any part of the subfloor. A thin pad is placed between the wood flooring and the subfloor. Then a recommended wood glue is applied in the tongue and groove of each plank to hold the planks together. The padding has its advantages: it protects against moisture, reduces noise transmission, is softer under foot, and provides for some additional "R" value. Some engineered floors and all Longstrip floors can be floated.
Glue Down
The recommended mastic or adhesive is spread on with the proper sized trowel to adhere the wood flooring to the subfloor. You should know that engineered wood floors and parquets can be glued down. Solid strip floors and plank floors can only be nailed or stapled.
Graining
Each wood species has its own unique graining and texture. The graining on the boards is determined by the way it has been cut. Natural variations in the color and grain are normal and to be expected.
Janka Hardness Test
This wood hardness rating test measures the force needed to embed a .444 inch steel ball to half its diameter in a piece of wood. The higher the number the harder the wood. Although this is one of the best methods to measure the ability of wood species to withstand indentations, it should be used as a general guide when comparing various species of wood flooring.
Knot
On a piece of wood, the round, harder, usually darker in color, cross section of where the branch joined the trunk of the tree.
Laminate
Laminate is a manufactured product that simulates the look of hardwood, ceramic tile, natural stone and many other types of flooring.
Long Strip Plank
One of the three common types of wood floors. (Others are Engineered and Solid.) Long Strip Plank floors are similar to Engineered floors and have several wood plies that are glued together. The center core is generally a softer wood material and is used to make the tongue and groove. A hardwood finish layer is glued on top of the core. The top layer can be almost any hardwood species and is made up of many smaller individual pieces that are laid in three rows. This gives the effect of installing a board that is 3 rows wide and several planks long. Long Strip floors come in a wide variety of domestic and exotic hardwood species and when damaged they are easy to replace.
Moisture Cured Urethane
A similar chemical make up as solvent-based urethanes, but this finish needs the humidity (moisture) in the air to cure.
Moldings
Are used to cover expansion joints and to enhance the performance and appearance of the hardwood floor. In many cases, moldings and baseboards need to be removed for hardwood installation.
Nail Down
This method is typically used with the 3/4" solid products, however there are adapters available for thinner flooring sizes as well. 2" nailing cleats are used with a wood flooring nailer and mallet to attach the flooring to the subfloor.
Number 1 Common
A quality of oak. Number 1 Common Oak has more knots and more dark graining.
Number 2 Common
A quality of oak. Number 2 Common Oak has more knots and more dark graining.
On-Grade
A cement slab that exists on the same plane as the surrounding terrain.
Plank
When shopping for a hardwood floor you will see boards in various sizes. The narrower board widths are referred to as “strips” and the wider units as “planks.” When we think of solid wood floors we generally are talking about a 3/4" thick plank that is 2 1/4" wide. This is the classic strip wood floor, although it is possible to find a narrower width or a slightly thinner gage. The strips are generally in random lengths from 12" – 84".
Polyurethane
A clear, tough and durable finish that is applied as a wear layer.
Pre-Finished Wood Floor
Pre-finished hardwood flooring comes ready for installation in your home. The hardwood boards have already been sanded, stained and finished at the manufacturing plant. In many cases this can provide a harder, better- protected surface. Several coats of urethane are sprayed on the boards and then they are UV dried for a very durable finish. Pre-finished floors offer a wider variety of wood species and save hours of labor and cleanup. They also may be screened and recoated to rejuvenate the finish and revitalize the floor’s natural beauty.
Rotary Cut
Each species has its own unique graining and texture. The graining on the boards is determined by the way it has been cut. Rotary Cut is a cutting process that displays a larger and bolder graining pattern.
Select
A quality of oak. Select Oak has some small knots and very little dark graining.
Sliced Cut
Each species has its own unique graining and texture. The graining on the boards is determined by the way it has been cut. Sliced Cut is a cutting process that shows a more uniform pattern.
Solid
One of the three common types of wood floors. (Others are Engineered and Longstrip Plank.) Solid wood floors are one solid piece of wood that have tongue and groove sides. When we talk about solid wood floors, we tend to think of floors that are unfinished, but it’s important to know that there are also many pre-finished 3/4” solid wood floors. Solid wood floors are sensitive to moisture and because so they are used in nail down installations and are not recommended for installation below ground level, or directly over a concrete slab.
Solvent-Based Urethane
Oil is used as part of the chemical make up of the polyurethane finish.
Square Edge
The edges of all boards meet squarely creating a uniform, smooth surface that blends the floor together from board to board.
Stapled Down
With this method 1-1/2 to 2 inch staples are used versus nailing cleats to attach the wood flooring to the subfloor. A pneumatic gun is used to drive the staple into the wood flooring and subfloor.
Strip
When shopping for a hardwood floor you will see boards in various sizes. The narrower board widths are referred to as “strips” and the wider units as “planks.” When we think of solid wood floors we generally are talking about a 3/4" thick plank that is 2 1/4" wide. This is the classic strip wood floor, although it is possible to find a narrower width or a slightly thinner gage. The strips are generally in random lengths from 12" – 84". The most common wood species used for solid strip floors are red oak, white oak, maple, cherry, white ash, hickory or pecan.
Tongue and Groove
The joining of two boards, one board having a tongue on its edge that fits into a groove in the edge of the other.
Trim
See Moldings.
Un-Finished Wood Floor
An Un-Finished wood floor allows you to have a custom job – you choose the wood species and it’s sanded and the stain is applied on site. With Un-Finished you also have the chance to level the surface of the entire floor after it has been installed.
UV Cured
Factory wood finishes that are cured with Ultra Violet lights versus heat.
Water-Based Urethane
Water is used as part of the chemical make up of the polyurethane finish.